Students have been busy with various tasks during the summer break. In addition to the activities shown below the Functional Testing team has been very active sorting out bugs and glitches and verifying correct functioning of subsystems. The Onboard Software team has met on-line every Friday (except one) all summer long to discuss tasks.
1 June – water-jet cutting of vibration adapter plate
The work was carried out at the KTH Prototype Center.
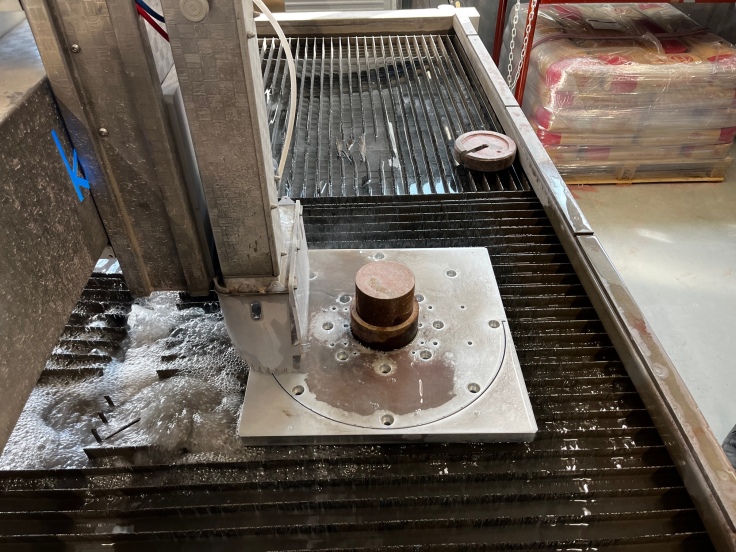


8 June – Practice vibration test
A dummy satellite weighing 2 kg composed of the fit check model of the SEAM Cubesat with a steel mass added on the inside was used as a test specimen. The purpose was to get acquanted with the vibrator and the vibration test acdaoter as well as the instrumentation. The test was carried out on the KTH campus at the Marcus Wallenberg Laboratory (MWL) at Teknikringen 8.



22-24 June – Satellite Integration Rehearsal
This was carried out at the MIST Integration Lab at Teknikringen. The flight structure was used together with 3D-printed mock-ups of all subsystems and experiments as well as physcally flight-representative electrical harness.


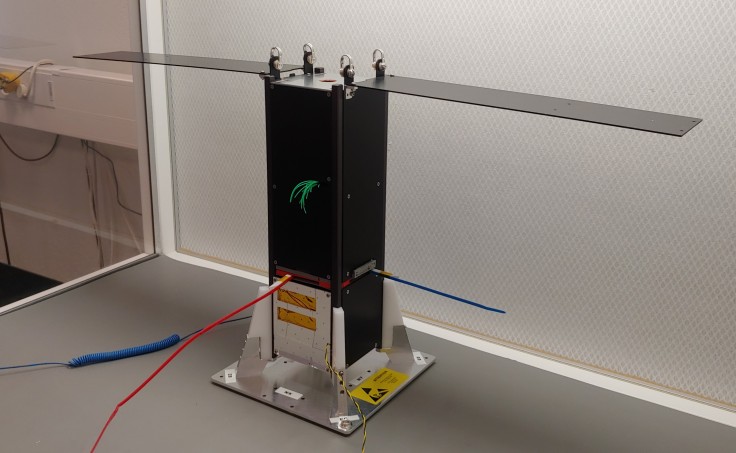

26 June – Rig for the communications and deployment test
For testing the deployment of solar panels and antennas as well as simulating the bringing into use of the satellite in orbit a special test is planned. The satellite is partially assembled and the deployable items (the Hold-Down and Release Mechanism – HDRM for the solar panels, and the Antenna System – AntS) are placed so that they can be easily removed and refurished after the test. The satellite mock-up was used to rehearse setting up the test configuration.
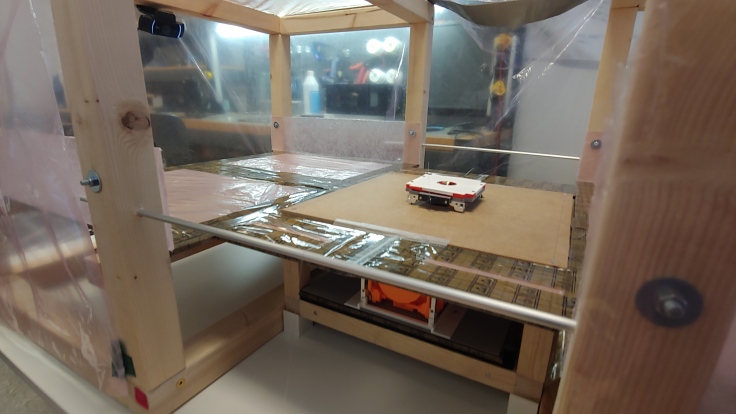
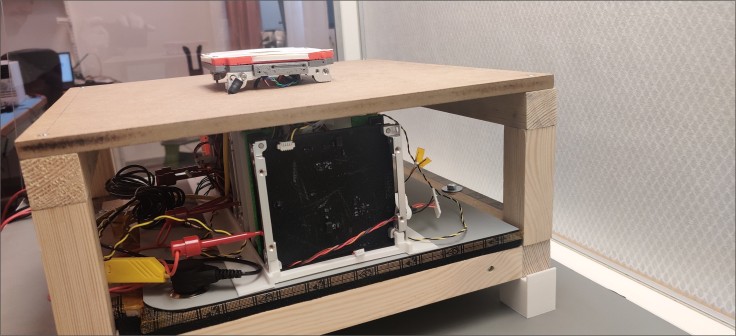
Leave a comment